As a business owner, the last thing you want to worry about is a broken oven. But the good news is that not all appliance repairs require a professional touch. In fact, with a little bit of DIY troubleshooting, you can easily diagnose and repair your commercial convection oven on your own!
However, to avoid the risk of serious injury, make sure to unplug your commercial convection oven before making any repairs. Wearing gloves is also recommended to help protect your hands.
Oven Not Heating Properly
If your commercial convection oven isn’t heating, it might have a broken igniter, malfunctioning bake element, or a faulty thermal fuse.
Broken Igniter
If the igniter is broken, your convection oven won’t ignite when needed, and you’ll need to replace the part. To do this, use the following steps.
- Unplug the oven.
- Remove the panel to access the igniter.
- Using needle-nose pliers, disconnect the two wires from the igniter.
- Remove the screws and bracket holding the igniter in place.
- Replace the old igniter with a new one.
- Using needle-nose pliers, reconnect the two wires to the new igniter.
- Secure the igniter with the bracket and screws.
- Replace the panel (using screws).
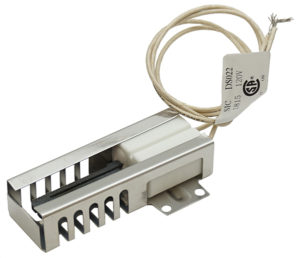
Malfunctioning Bake Element
Check the bake element for blisters or separation. If you can see any visible damage, you’ll likely need to replace the component entirely. To do this:
- Unplug the oven from its outlet.
- Remove any screws holding the bake element in place.
- Detach any wires connected to the bake element.
- Connect the new element to the same wires as the old bake element.
- Use screws to secure the new bake element in place.
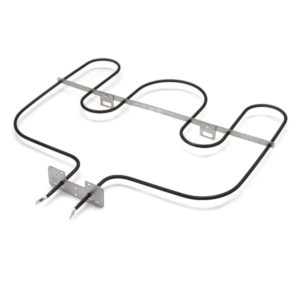
Faulty Thermal Fuse
To diagnose your unit’s thermal fuse, you can do this by using a continuity tester.
Touch the end of the thermal fuse with the continuity tester probe. If there isn’t an electricity flow, your convection oven likely needs a new fuse.
- Remove the oven’s back panel.
- Disconnect the two wires connected to the thermal fuse with needle-nose pliers.
- Remove the thermal fuse from the oven.
- Replace the old thermal fuse with a new one.
- Reconnect the two wires using needle-nose pliers.
- Secure the panel back onto the convection oven.
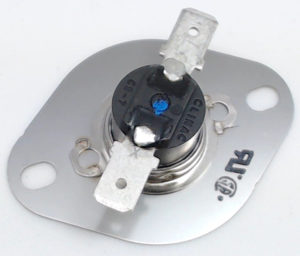
Improper Temperature
If your oven doesn’t reach the right temperature, it might have a broken temperature control thermostat, malfunctioning oven control board, or broken convection element.
Let’s review the steps to check and repair these simple, yet inconvenient issues.
Broken Temperature Control Thermostat
- Unplug the convection oven from the wall.
- Unscrew the panel from the back of the oven.
- Using needle-nose pliers, remove the wires connected to the thermostat.
- Remove screws holding the thermostat in place.
- Unclip the thermal bulb from inside the oven.
- Push the thermal bulb back through the oven to remove the thermostat.
- Clip the new component to the inside of the oven.
- Using needle-nose pliers, secure the wires to the thermostat.
- Secure the thermostat with screws.
- Put the panel onto the back of the oven.
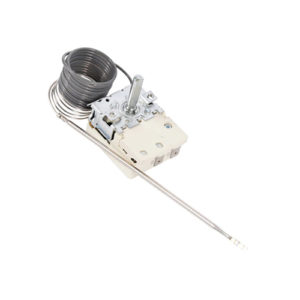
Malfunctioning Oven Control Board
First, try tightening the screws around the control board to ensure this isn’t causing your problem. If loose screws aren’t the problem, you may need to replace the oven control board.
- Turn off the power to the oven.
- Unscrew the control board from the oven.
- Lift the control board out.
- Disconnect the wires from the oven control board.
- Replace the old control board with a new control board.
- Reconnect the wires to the new board.
- Set the control board back into the oven.
- Use the screws to secure the control board in place.
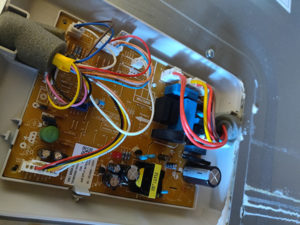
Broken Convection Element
The convection element is found at the back of your oven. It is the fan that helps to circulate and distribute heat evenly. You can check and test the fan by turning on your convection oven. If the fan doesn’t spin, you know you need a new one. However, this repair involves many wires and, in most cases, electrical repair.
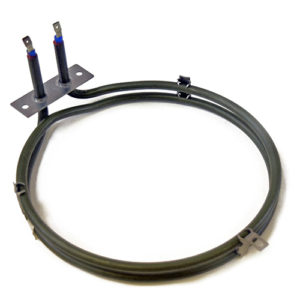
Oven Bakes Unevenly
Let’s say your commercial convection oven heats properly but isn’t baking evenly. In this case, you’ll want to check the temperature sensor and broil element to try and diagnose your issue.
Faulty Temperature Sensor
Start by visually inspecting your temperature sensors to make sure your commercial convection oven’s temperature sensor isn’t bent out of place or broken. If necessary, reposition the sensor so that it does not touch the oven wall. Next, check the temperature sensor using a multimeter.
If the tester is unable to identify a current at the sensor, you’ll likely need to replace it with a new one.
- Unplug the convection oven from the outlet.
- Remove the back panel of the oven to gain access to its internal components.
- Unscrew the temperature sensor.
- Using needle-nose pliers, pull the wire from the temperature sensor.
- Pull the sensor out of the oven.
- Feed the new sensor into the oven.
- Re-attach the wire using needle-nose pliers.
- Secure the temperature sensor with the bracket and screws.
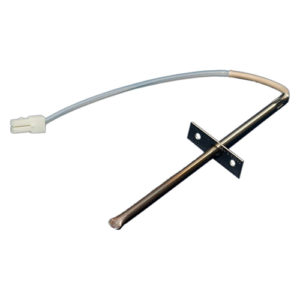
Faulty Broil Element
A faulty broil element will look blistered and damaged. If this is the case, replace your convection oven’s broken broil element with a new one.
- Make sure the power is off.
- Remove the screws and brackets holding the broil element.
- Locate the wires that connect the element to the convection oven.
- Remove the broil element from the wires using needle-nose pliers.
- Replace the old element with a new element.
- Reconnect the wires using needle-nose pliers.
- Use the screws and brackets to secure the new broil element in place.
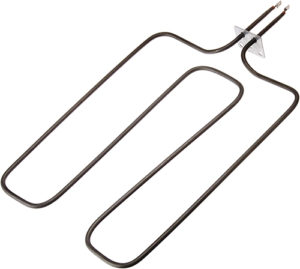
Leave a Reply